Modern CNC lathe machines normally include tools that could deal with multiple axes. Various types of machines can include both X and Y-axis, incorporate a 2nd turret with other tools, or consist of a second spindle. This suggests a CNC lathe can carry out additional milling, drilling, and tapping operations, leading to a complete and even complex part manufacturing process and removing the need to transfer the part to another machine for a second operation. This article takes a look at the different types of CNC lathes, their applications, and factors to consider.
Separate from the main spindle as a choice, the sub-spindle works in sync with the main spindle to finish the first and 2nd cutting operation in a CNC lathe. This improves efficiency and throughput per cycle. When named as a second spindle, the system has the same capability and power as the main spindle.
Comprising the primary motor, the headstock holds the primary spindle where the chuck is mounted on. To make sure high performance, you require to think about if your machine tool’s headstock can deal with high torque at low speed. This is an essential consideration for difficult products. Tailstock are used to provide an extra support force on the other end of the element. This is essential when machining long and extra-long work pieces (e.g. Shafts).
CNC Turning is a manufacturing process in which bars of material are held in a chuck and turned while a tool is fed to the piece to get rid of material to produce the desired shape. A turret (shown center), with tooling attached is set to transfer to the bar of raw material and eliminate material to develop the set outcome. This is likewise called “subtraction machining” because it involves material elimination. If the center has both tuning and milling abilities, such as the one above, the rotation can be stopped to allow for milling out of other shapes.
A chuck is a vice-like structure that grips the workpieces to be machined. It is attached to the main spindle that rotates both the chuck and the workpiece. To attain greater performance in production, you should think about CNC lathes that offer a range of choices, enabling you to switch to the ideal tool for your turning jobs. Some of CNC machine tools have the flexibility and size to accommodate extra-long oil pipe machining and other long shaft applications.
Run with Computer System Numerical Control (CNC) systems and provided with accurate design instructions, CNC Lathes are machine tools where the material or part is clamped and turned by the primary spindle, while the cutting tool that deal with the material, is mounted and moved in various axis. CNC Lathes are usually used for machining parts, where the material/ part is secured and turned whereas the cutting tool is stationery installed for OD (External Diameter) and ID (Inner Size) operations, e.g. shafts and pipes. They are ideal for parts that have same symmetry around an axis that could be chucked up (i.e. radially clamped) in the spindle.
A lathe is generally used in woodturning, metalworking, metal spinning, thermal spraying, parts reclamation, and glass-working. One or two centers generally hold the workpiece, and at least one center can be moved horizontally to accommodate workpieces of different lengths. CNC lathes are rapidly changing older production lathes due to their ease of setting, operation, repeatability, and precision. CNC lathe work is just one kind of CNC machining. However what is a CNC lathe? First, CNC represents computer mathematical control and refers to a machine operated by a computer system. A CNC lathe is run with accurate style guidelines to machine parts to accurate specifications. A CNC lathe is a machine tool where the material or part is held in location and rotated by the main spindle as the cutting tool that deals with the material is installed and carried on different axes.
An easy CNC Lathe operates on 2-axis and the tool lies in a fixed position at 8 to 24 station turret. The rotating action of the part is called “turning”, for this reason specific types of CNC Lathes are called CNC Turning Machines. Milling (cutting tool moves around stationery workpiece), uninteresting and tapping (a tool that cuts threads inside hole) tools are generally driven by a separate drive system inside the turret. Depending on the application, the life tools (i.e. active tool) are mounted for axial or radial functional instructions. These could be found in 3-axis CNC Lathes or CNC Turning Machines.
Lathe machines with additional options such as Y-axis, sub-spindles, or particular picked alternatives for automation are commonly called Turning Centres. These sophisticated machine tools are capable of machining complex parts– these surpass standard OD & ID turning operations and might include milling, drilling and tapping operations to finish the part in one setting. Taking a piece from raw part to finished item, such all-in-one machine tools substantially improves efficiency.
Often referred to as the heart of a machine tool, the main spindle consists of a spindle assembly and the spindle drive system. These are some of the moving parts of the CNC machine tool, and they consist of motors, gears, and the chuck (more on it later on). The C-axis drive which assists to position the material will also be assembled together with the spindle. Tool holders are typically set up at the turret disk (a rotating disk allowing tools to be positioned and changed), they include both fixed and life tool holders. The life tool drive system is integrated.
A simple CNC lathe operates on two axes with the cutting tool in a set position at 8 to 24 station turret. The turning action of the workpiece is called “turning.” automatic cnc lathe This is why particular kinds of CNC lathes are called CNC Turning Machines. CNC lathes produce exact round shapes with an external size (OD) and an inner diameter (ID). Various type of structures can be machined with this machine tool, depending on their numerous markets’ needs. They are commonly utilized in oil and gas, automotive, aerospace, medical, electronics, mining, power plant, steel and paper mills, and shipbuilding markets.
Subscribe to Updates
Get the latest creative news from FooBar about art, design and business.
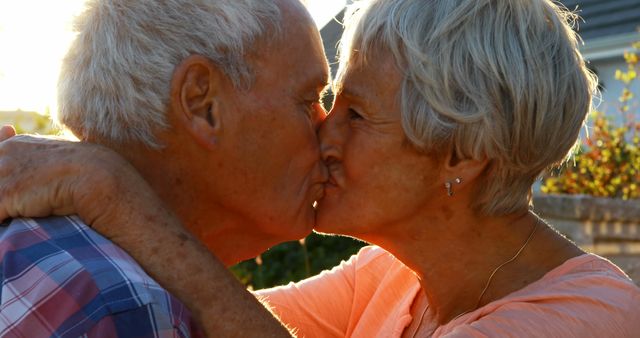