Another aspect to consider is the material made use of for tower packing. Typical products consist of metal, plastic, and ceramic, each offering different advantages. inclined tube settler is durable and can stand up to heats and stress, making it suitable for demanding applications. Plastic packing, on the other hand, is lightweight and resistant to deterioration, making it perfect for processes including aggressive chemicals. Ceramic packing provides high thermal security and resistance to chemical strike, making it appropriate for specialized applications.
The height and diameter of the tower are also crucial design considerations. The tower’s height influences the house time of the phases, permitting adequate mass transfer. Nonetheless, a taller tower may lead to increased pressure drop, demanding an equilibrium between height and efficiency. The diameter, on the other hand, influences the flow rates and the distribution of phases within the tower. A bigger diameter can accommodate higher flow rates, however it may also lead to obstacles in keeping uniform flow distribution, which is essential for efficient mass transfer.
In addition to the design and material considerations, regular maintenance of the tower packing system is vital for maintained performance. Gradually, packing material can come to be fouled or degraded, leading to minimized mass transfer efficiency and increased pressure drop. Regular evaluations and maintenance methods can assist identify potential issues before they escalate, ensuring that the tower remains to run successfully. Cleaning up or replacing packing material as needed can significantly improve the longevity and efficiency of the system.
The packing material made use of in towers is generally developed to offer a big surface for communication between the phases while minimizing resistance to fluid flow. This is essential since the efficiency of the mass transfer process depends on the effective contact between the gas and liquid. There are various types of packing products available, including random packing, structured packing, and ceramic packing, each with unique characteristics that make them suitable for different applications. Random packing, such as raschig rings or pall rings, is composed of small, off-and-on shaped items that are placed in the tower haphazardly. This kind of packing permits adaptability in operation, as it can suit a variety of flow rates and operating conditions. Nevertheless, the random setup may lead to irregular flow distribution and pressure decreases.
In conclusion, tower packing is an essential aspect of various industrial processes that rely on mass transfer for separation. The selection of packing material, design considerations, operating conditions, and regular maintenance all play a crucial function in making certain the efficiency and effectiveness of the packing system. As markets remain to evolve and seek extra efficient separation techniques, improvements in tower packing innovation will continue to be essential for attaining optimal performance in mass transfer procedures. Whether in chemical manufacturing, oil refining, or wastewater treatment, understanding and maximizing tower packing systems will certainly add significantly to enhancing efficiency and sustainability in various industrial processes.
The performance of tower packing can be assessed making use of various parameters, including height equivalent to a theoretical plate (HETP), pressure drop, and mass transfer coefficients. HETP is a crucial statistics in distillation and absorption processes, showing the efficiency of the packing material. A lower HETP value indicates an extra effective packing, permitting much better separation with fewer theoretical phases. Pressure drop, on the other hand, is an essential consideration in the design of the tower, as excessive pressure drop can lead to increased power consumption and lowered functional efficiency.
Structured packing, on the other hand, is developed with a specific geometric shape to enhance flow distribution and mass transfer efficiency. The structured packing consists of slim sheets or layers that are prepared in a specific pattern, producing a bigger surface for communication. This sort of packing can significantly minimize pressure drop compared to random packing while improving mass transfer performance. Its design also facilitates far better water drainage, decreasing the probability of flooding or crying, which can adversely influence the separation process.
Tower packing is a critical element in various industrial processes, specifically in chemical and petrochemical sectors. It plays a substantial duty in mass transfer procedures, where the goal is to separate components of a blend based upon differences in their physical and chemical residential or commercial properties. This strategy is primarily utilized in distillation, absorption, extraction, and other separation processes. Tower packing entails filling an upright column or tower with packing material that improves contact between the liquid and vapor phases, therefore boosting mass transfer efficiency.
When making a tower packing system, a number of factors must be thought about to make sure optimal performance. The first consideration is the kind of separation process being utilized. Different processes have varying needs in terms of mass transfer efficiency, pressure drop, and capability. As an example, a distillation column may call for a different packing design compared to an absorption tower. Comprehending the specific demands of the process assists in choosing the suitable packing material and arrangement.
An additional vital aspect to think about is the operating conditions within the tower, including temperature level, pressure, and flow rates. These conditions can significantly impact the performance of the packing material. As an example, high temperatures can lead to thermal expansion of the packing, potentially causing blockages or increased pressure drop. In a similar way, variations in flow rates can lead to flooding or poor contact between the phases, impacting general efficiency. As a result, it is essential to carefully keep an eye on and manage these specifications during procedure to ensure optimal performance.
Subscribe to Updates
Get the latest creative news from FooBar about art, design and business.
7 Beautiful Explanation We Can’t Help But Fall In Love With Industrial Tower Packing
5 Mins Read
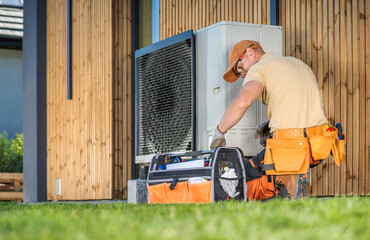