Amongst synthetic resins, lots of analysts try to distinguish in between barrier resins and structural resins utilized in packaging. By specifying some limits of gas permeability that make up barrier residential or commercial properties, resins are placed in one or the other category. BCC Research does not strictly categorize barrier packaging resins in this way, for not just is “barrier” an approximate term, however different resins can perform both barrier and structural functions in some plastic packaging structures. All resins talked about and evaluated in this report are considered to be barrier resins, even if their use may primarily be structural in many or most of their packaging structures.
Despite the fact that much of the fundamental innovation of barrier plastics is the same, we discovered that development had actually continued to be made in the few years because the last BCC Research report on this subject. One topic that continues to get attention is plastic packaging for beer, with new technologies unveiled and promoted. Beer is a really challenging product to bundle because of its high level of sensitivity to quick taste destruction from direct exposure to oxygen, At this time, at least in the United States, barrier polyethylene terephthalate (PET) beer bottles have not shown that they can supply the extended life span that glass and aluminum can, except for short shelf-life beer for sports events and so forth. However work continues by barrier packaging firms and beer bottlers that want plastic beer bottles.
Metals such as tinplate (tin covered steel) and aluminium are used in can and tray manufacture. Metal packaging offers the longest service life and remarkable safety for foods and beverages by preventing microorganisms, light and oxygen from damaging the item inside the container. Metal can be manufactured into the standard three-piece can, which includes a base, cylinder and cover; or a two-piece can, consisting of a base and cylinder in one piece and a lid without a seam.
The general pattern of rust in lacquered cans is different from that in plain cans, and is typically more complicated. It depends not only on the quality of the base steel plate, the tin– iron alloy layer and the tin finishing, but likewise on the passivation layers and the nature of the lacquered coating. The effectiveness of a lacquer finish is related straight to its ability to function as an impermeable barrier to gases, liquids and ions, consequently preventing corrosive action on the protected surface.
Due to their flexibility, variability in size and shape, thermal stability and barrier homes, plastic packaging products is the fastest growing sector, changing the traditional materials of glass, metal, paper and board. In general, the permeability of plastic packaging depends on its attributes such as crystallinity, molecular orientation, chain tightness, free volume, cohesive, permeate residential or commercial properties such as molecule size and nature and external conditions.
Standard packages (glass containers, metal cans) in addition to plastic bottles, and laminates (such as paper laminated with aluminium foil) supply an appropriate barrier to oxygen. Nevertheless, some distinctions exist in between the numerous packaging systems. In the case of metal cans and glass containers, these can be considered impermeable to the passage of gases, odours and water vapour. Plastics-based packaging materials provide differing degrees of security, depending mostly on the nature of the polymers used in their manufacture.
All packaging offers some sort of barrier; this is a primary reason for packaging products in the first place. Packaging protects products from seepage (or, sometimes, exfiltration, the latter the death of a material or materials out of the container) of impurities, of flavor, color, smell, and so on, in addition to maintaining the contents. Glass and metal containers have been used for packaging products for many years and definitely qualify as barrier plans. As we discuss later on, thick glass and metal qualify as “practical” barriers that stop almost whatever from travelling through them.
Packaging has actually been around for centuries, and most likely was developed for a number of factors. These consist of conservation and stability of items gradually and the protection of products from damage, dirt, moisture, and so on. Early packaging was quite unrefined (e.g., the casks and cases of salted meat carried on old sailing ships, which frequently went to sea for extended lengths of time).
plastic barrier packaging and lacquered tinplate cans are used for food and drink packaging. Plain internal tinplate cans are utilized for specific food types (white fruits (e.g. pineapple, pear) and some vegetables (e.g. mushrooms, asparagus)). The presence of a bare tin surface inside the can results in security of the natural flavour and appearance of the food, through oxidation of the tin surface in preference to oxidative degradation of the food. This process keeps the quality attributes that customers get out of these items throughout the entire shelf life. Among the downsides of metal cans is that they are prone to rust.
Subscribe to Updates
Get the latest creative news from FooBar about art, design and business.
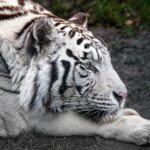